How Rotary Engines Work?
A Wankel rotary engine is an internal combustion engine that uses a rotary design to convert pressure into a rotating motion – it can be viewed as a device part-way between a reciprocating piston engine and a turbine. German engineer Felix Wankel began developing the concept of the Wankel rotary engine in the 1920s. However, the known design was developed by NSU and patented by Walter Froede in 1960. This design is characterised by a triangular rotor that revolves around a central eccentric shaft. The combustion occurs in the pockets formed between the rotor and the housing.
The Wankel rotary engine has a few key advantages over traditional piston engines. One of the main benefits is its compact size and lightweight design. The rotary engine has a relatively simple design with fewer moving parts, making it more reliable and easier to maintain.
The Wankel rotary engine’s high power-to-weight ratio makes it an ideal candidate for Unmanned Arial Vehicle (UAV) propulsion systems and other applications, including hybrid automotive and auxiliary power units.
Principles of Rotary Engine
The Wankel rotary engine is based on a unique design that uses a triangular rotor that rotates around a central shaft. The rotor had three sides, each acting as a separate combustion chamber. As the rotor turns, it creates a four-phase cycle similar to a traditional piston engine.
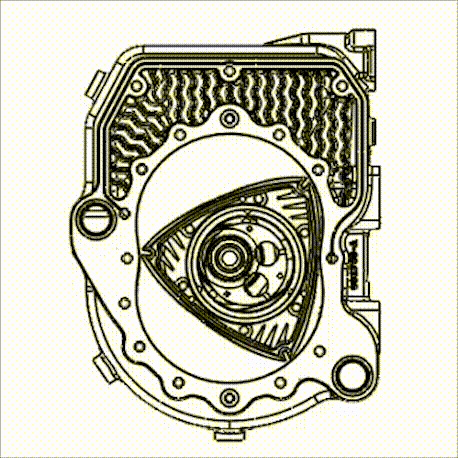
The Wankel rotary engine operates on a four-phase intake, compression, power and exhaust cycle. However, unlike a reciprocating piston engine, where all these cycles happen in the same chamber in a Wankel rotary engine, these cycles occur in separate areas within the engine. The rotary engine converts the pressure produced by the combustion of the fuel-air mixture into rotational motion, which is then used to power the vehicle.
What are the main components of a Rotary Engine?
The number of components within the Wankel rotary engine is minimal compared to the reciprocating engine. The following are the major components of a Wankel rotary engine.
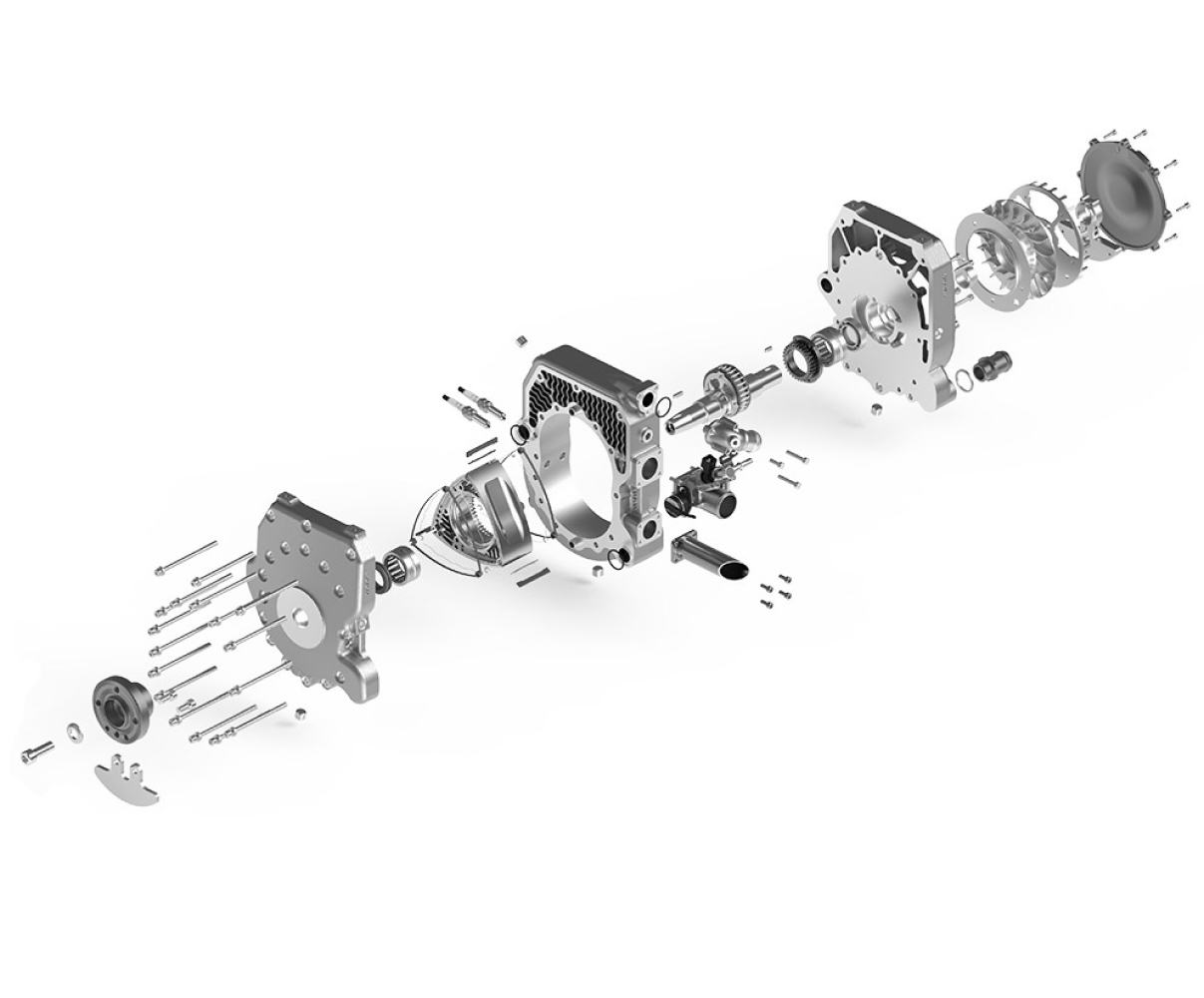
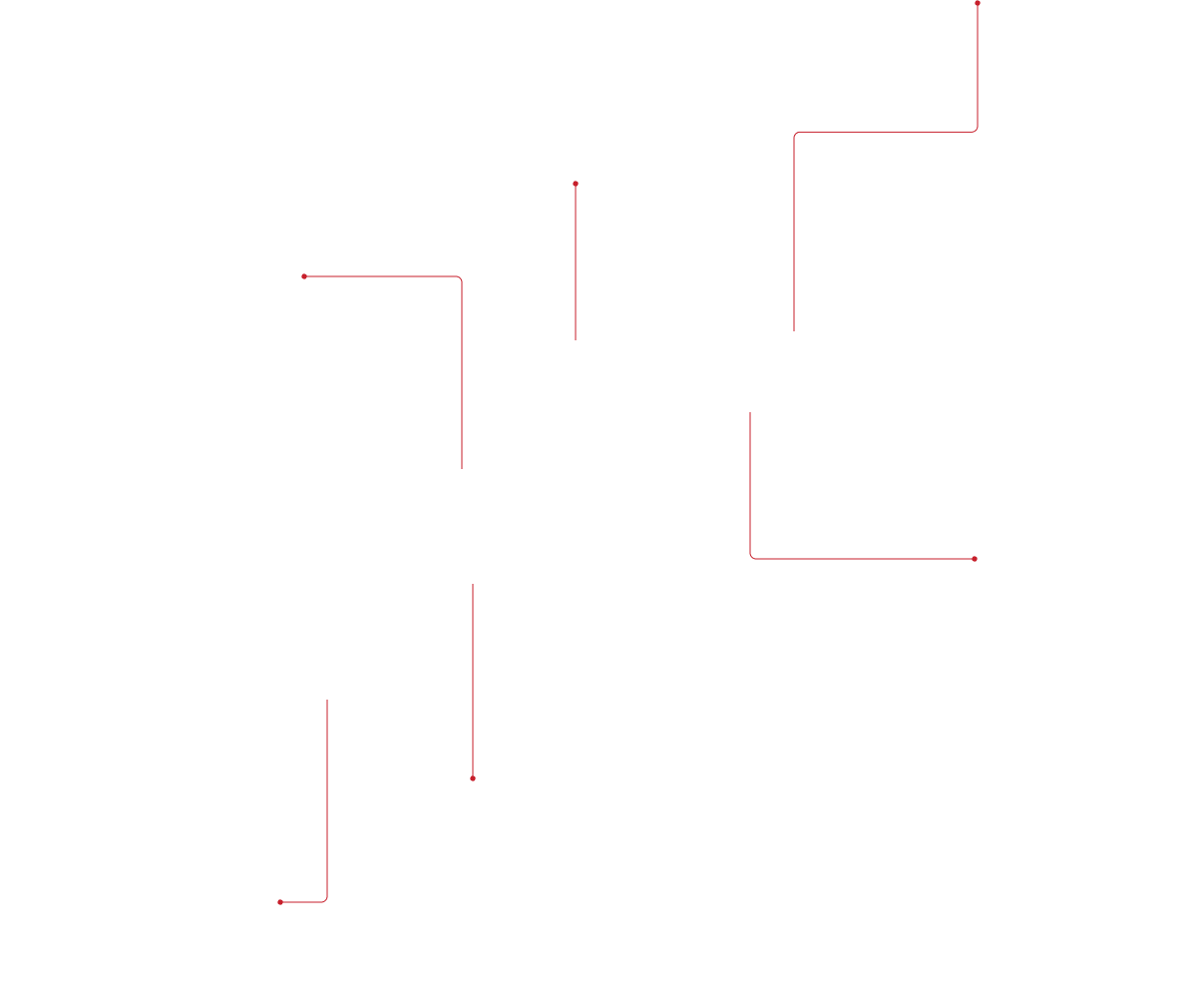
Rotor
The rotor is one of the main components of the Wankel rotary engine. It is an equilateral triangular shape with three apices and convex-curved faces that rotate around the eccentric output shaft. Each side of the rotor acts as a separate combustion chamber. The curved faces of the rotor reduce the displacement, hence attaining the highest possible compression ratio.
Rotor Housing
In addition to the rotor, the rotor housing is a vital part of the Wankel rotary engine. It is a figure of an eight-shaped (epitrochoid) enclosure with which all three rotor tips are always in touch, forming the three distinctive combustion chambers. The housing is, therefore, essential as it is necessary to complete (or enclose) each part of the combustion process, including intake, compression, combustion, and exhaust.
Stationary Gear
A fixed gear is mounted on one side of the rotor housing and meshes with another gear attached to the rotor. These gears maintain correct phasing between the rotor and eccentric shaft, ensuring the rotor moves precisely through a one-third turn for each drive shaft turn. Interestingly, the gear ratio of the rotor gear to the fixed gear is 3:2, with the remaining third being a function of the eccentric motion.
Side housings / Endplates
Two end plates, with which the rotor side seals are always in contact, serve to enclose the working chambers and support the eccentric shaft. One of the endplates has the stationary gear attached, which meshes with the gear on the rotor.
Seal Packs
Adequate sealing is required to reduce unwanted gas leakage between each chamber within the engine, which is crucial for the engine’s power, efficiency and reliability. The Wankel rotary engine seals function similarly to the piston rings in conventional piston engines. There are two paths for the gas to leak between each face of the rotor; hence, it has two types of seals: side and apex.
Eccentric Output Shaft
The eccentric shaft has a circular lobe mounted eccentrically, offset from the shaft’s centre line. The rotor runs on and has its path defined by the lobe, which ensures all three apices’ faces are in constant touch with the rotor housing.
Combustion Cycles of a Wankel Rotary Engine
The Wankel rotary engine operates on a four-phase combustion cycle.
1
Intake
The intake phase starts when the leading rotor apex passes the intake port on the rotor housing. Air and fuel are induced into the chamber as the rotor rotates with the intake port open. Once the rotor apex passes the port opening, the section becomes sealed and ready for compression.
2
Compression
Once the intake phase is completed, the rotor continues its eccentric motion through the rotor housing by reducing the volume of the chamber and compressing the air-fuel mixture. The chamber reaches its minimum volume as the rotor reaches the spark plugs.
3
Combustion
The engine’s spark plugs ignite the compressed air-fuel mixture just before minimum volume. The ensuing pressure generated by the expanding gases of the explosion pushes onto the rotor flank, causing rotation. This pressure on the rotor’s flank creates torque and engine power.
4
Exhaust
The exhaust phase is the final phase of the cycle. In this phase, the rotor continues to rotate after combustion, squeezing out the gasses created during the previous phase. The gasses exit the chamber through the exhaust port. Once the exhaust cycle completes, the new intake phase starts, and the cycle repeats.

AIE’s world-class 225CS – 40 BHP UAV engine Wankle rotary engine
The world-class 225CS – 40 BHP rotary engine that delivers market-leading performance in terms of power, weight, efficiency and reliability.
Advantages of a Wankel Rotary Engine
There are several advantages to using a Wankel rotary engine, including the following:
Compact size
The Wankel rotary engine is compact, making it ideal for small aerial vehicles.
Lightweight
The Wankel rotary engine is lightweight, which can help improve the vehicle’s overall performance and fuel efficiency.
Simple design
The Wankel rotary engine has a relatively simple design with fewer moving parts than a traditional piston engine, making it more reliable and easier to maintain.
High power-to-weight ratio
The Wankel rotary engine has a high power-to-weight ratio, meaning it can produce much power relative to its size and weight. This high power density can make it an attractive option for use in high-performance UAS.
Smooth (low vibration) operation
The Wankel rotary engine is perfectly balanced by design, making it a perfect choice for UAVs with optical payloads.
Multifuel capabilities
Wankel rotary engines are known for their flexibility and ability to run on various fuels, including gasoline, heavy fuels, kerosene, diesel, and alternative fuels such as ethanol and natural gas.
About Advanced Innovative Engineering
Advanced Innovative Engineering (AIE) specialises in designing and developing Wankel rotary engines. Founded in 2012, AIE is headquartered in Lichfield, United Kingdom, and has a reputation for producing high-quality rotary engines for various applications.
AIE’s Wankel rotary engines are known for their compact size, lightweight design and high power-to-weight ratio.
They are well-suited for various applications, including racing, aviation and marine use. In addition to designing and manufacturing rotary engines, AIE also provides engineering and consulting services around rotary engine technology to help customers develop custom solutions for their specific needs.
If you would like to find out more about AIE’s product range, please visit: www.aieuk.com/products